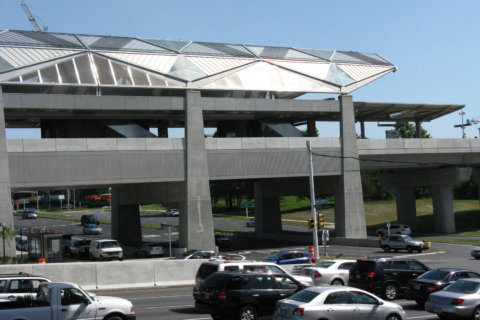
WASHINGTON — The company that provided faulty concrete panels for Silver Line stations says it dismissed warnings about falsified quality control records as simply the complaints of disgruntled employees, and that any issues are not significant enough to warrant paying damages since problem panels are now being addressed.
Universal Concrete Products and its president and co-owner Donald Faust filed their first formal responses this week to a whistleblower lawsuit backed by the federal government and state of Virginia.
The company blames a “rogue employee” for changing quality control records, and said workers who left the company due to poor performance were the ones who raised concerns.
Concrete panels made by the Pennsylvania company under a $6.1 million subcontract did not have the proper mix of air inside to prevent premature breakdown. Since the issue became apparent last year to the Metropolitan Washington Airports Authority as part of separate construction oversight, the company and lead construction contractor Capital Rail Constructors have agreed to pay for sealant to regularly be put on the 1,587 station framing panels to extend their useful life to the required 100 years.
“There is no concern that the panels are not safe; the only concern is whether the panels will last the expected lifetime. The sealant allays that concern,” Universal Concrete Products said in its answer to the lawsuit.
This whistleblower lawsuit was initially filed in 2016 but was not unsealed until earlier this year.
Many of the panels installed at the stations due to open in 2020 had to be removed entirely, while others are simply getting the sealant.
In its response to the lawsuit, Universal Concrete Products denies that it knowingly made false statements or used false records to support its panels.
A now-former employee who was at one point the company’s quality control manager has already pleaded guilty in the case to conspiracy to commit wire fraud.
He said many of the panels produced for the Silver Line beginning in late 2015 fell short of required standards, but that he and other employees were expected to record false results that made it appear they met requirements.
“We cannot give them sheets with any testing data out of specs. They will reject those panels. We have to change the data,” Andrew Nolan wrote to Nathan Davidheiser in December 2015.
Nolan is due to be sentenced next week.
Davidheiser is the person who ended up filing the whistleblower lawsuit.
In a separate response to an individual complaint filed by Davidheiser, the company admits he protested instructions to perform quality control tests. The company argues he voluntarily resigned though, and was not fired in retaliation for protected complaints.
The company and Faust say they only learned later of the problems with panels and deny that the problems were “consistent”.
“UCP had no knowledge and did not condone changing any data in any records,” their response to the lawsuit said.
The company also denied that any records contained falsified air content results, and said that given the new sealant applied to panels they do meet contract specifications.
“UCP would not have delivered panels had it known that a rogue employee was changing records,” the response continued.
In September 2015, a worker named Omar Gonzalez told Faust that “everybody on the floor” knew Nolan had been “cooking the books of the lab testing procedures.”
The company now says it fired Gonzalez a week later “for poor job performance”.
“Gonzalez’s statements were believed to be unreliable comments from a disgruntled former employee,” the company said in its response.
That December, another employee said quality control was cooking the books and he had pictures to prove it.
A manager recommended that worker have his pay cut or be fired.
The company now says that recommendation was not based on the quality control complaints, but instead due to “repeated poor job performance” and a past failure of a certification test.
No further investigation was done into the complaints.
Two months later, in February 2016, Davidheiser raised concerns about quality control, including specifically on the Silver Line panels.
“I am being asked to constantly falsify data that we send out to our clients in order to appear that the concrete is in specification,” he wrote Feb. 17.
The company said the complaint was not linked to the specific panels for the Silver Line, and did not specifically say that the air ratio problems identified later were the issue.
Another manager who suggested further investigation was fired the following week, before any new internal audit could be conducted.
Faust’s legal response filed this week said the firing was not related to the quality control allegations or investigation.
The company referred the issues to Nolan, who did not raise any issues with the Silver Line panels, the response filed this week said.
The company denies that any falsification happened, if it did, any time after Jun. 2016.
The government charges the faked quality control records continued until at least Feb. 2017 when Silver Line inspectors identified issues with panels.
Separate concerns about incorrect stone used in the concrete mixes appear to have created no additional problems.