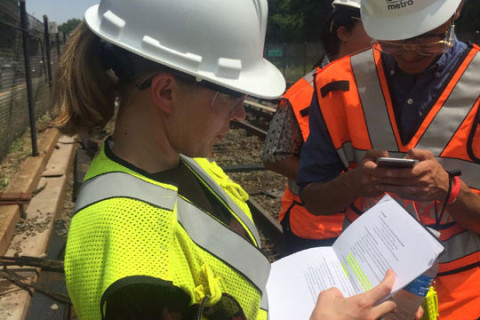
WASHINGTON — Metro is promising to improve worker safety and training issues after a series of internal reviews found room for improvement, and the Metro Board is also getting an update Thursday on new technology meant to be rolled out over the next several years to reduce the risk of workers getting run over on the tracks.
The National Transportation Safety Board recommended in 2008 that Metro implement automatic alert technology so that workers on the tracks and train operators are aware of potential collisions. Metro has now begun training for workers on a pilot system due to launch at 13 locations within the next year.
Elsewhere in the system, Metro has reduced the number of workers without required current track safety training certification over the last two years, largely by ending the training requirement for many workers who rarely or never needed track access.
Metro said a new system map highlighting the most dangerous areas for workers on the tracks has also been completed.
A safety stand-down is planned this summer to remind workers of new safety rule changes and emergency maintenance procedures.
Eight Metro workers were killed on the tracks between 2005 and 2010.
Internal reviews find worker safety issues, other challenges
A series of internal Metro reviews recently made public found worker safety issues ranging from a failure to inspect electrical safety gloves to a lack of training or first aid kits.
The Metro departments responsible for the issues have promised to fix the problems, which also include expired or missing inspections of lifts or cranes, tripping hazards such as open gaps in the floor, and a lack of procedures to ensure contractors and employees are up to date on required training and certifications.
Weight certifications that are required annually for lifts were expired or not available at all when Metro’s Quality Assurance, Internal Compliance & Oversight group checked for them this winter. A lift in the New Carrollton railcar maintenance facility had last been checked in March 2016. A West Falls Church lift did not have a certificate at all.
Separate monthly inspections had also not been done consistently. Out of 12 lifts randomly checked, only one was compliant.
Federal OSHA violations included a failure to train workers to inspect fall protection equipment, which meant there were no inspection records available.
In some cases, there was no evidence of any training at all for designated employees who are supposed to play key roles in safety incident investigations and reporting, and the safety department was not directly participating in meetings meant to help identify risks and trends. Those local or department safety committee meetings also did not appear to be going into as much detail as they should.
That gets in the way of meeting the Federal Transit Administration’s direction to ensure all safety incidents are entered into Metro’s safety measurement system.
In several areas, there were no records of any checks to be sure safety and maintenance rules were properly being followed; more than 200 pieces of equipment were not properly calibrated, and other equipment lacked evidence of current certifications.
Workers have also sometimes been left without the tools they need to do their jobs.
For example, Metro’s internal reviews found fare collection system maintenance workers doing maintenance without proper tools and using outdated checklists that do not properly track maintenance data.
The fare collection department also had missing supervisory reports and a need for upgraded maintenance policies, an internal review found.
Some of the issues found in the reviews were addressed within weeks, such as replacement of expired electrical safety gloves used at bus maintenance garages and fire extinguishers that were missing or had out of date inspections.
Electrical safety gloves and fire extinguishers were also not regularly inspected in rail yards, and logbooks were not properly maintained.
Metro railcar maintenance supervisors promised to immediately start inspecting all high voltage insulating gloves at the start of each shift, establish proper logbook procedures, and review the need for additional first aid kits.